Surface roughness is the main factor affecting the wide application of diamond films. Choosing a suitable polishing method can greatly reduce the surface roughness to accelerate the commercial application process. In this paper, a new polishing method, magnetic polishing, is proposed for the inner hole diamond film.
Diamond film has excellent performance and is an ideal coating for tool and mold materials. With the development of chemical vapor deposition (CVD) technology, the production cost of diamond film synthesized by this technology is significantly reduced, which has commercial application prospects. .
However, the orientation, grain size and thickness of the surface of the conventional diamond film are not uniform, and the surface roughness is also high, generally up to several micrometers, which affects many applications of the diamond film.
For example, diamond film coated tools and molds require a high surface finish, so diamond post-processing techniques (including polishing, leveling, metallization, etc.) are becoming more and more important.
For the polishing of diamond films, the polishing problem of diamond films has become a key technology for expanding the application of diamond films due to its high hardness, stable chemical properties, and thin thickness, and diamond film peeling is likely to occur during polishing.
In recent years, many scholars at home and abroad have proposed a number of new diamond film polishing methods through a large number of research and experiments, including chemical-assisted mechanical polishing, laser polishing, thermochemical polishing, ion beam polishing, and electric spark polishing. These methods basically utilize the diffusion and evaporation of carbon atoms and chemical reactions, micro-cutting, graphitization of the surface, etc. to achieve polishing of the diamond film. Since the "magnetic brush" of magnetic grinding is flexible, it is very suitable for the polishing of the inner hole. In this paper, a new method for polishing inner-hole diamond films by magnetic grinding is proposed. The surface morphology, quality and properties of the films before and after polishing are studied. The characteristics and effects of magnetically-polished diamond films are discussed.
Principle of magnetic grinding
As shown in Figure 1, a magnetic field is formed between the magnetic poles N and S. If the magnetic field is filled with an abrasive that has both magnetic and cutting ability, the abrasive will be closely and regularly arranged along the magnetic lines of force to form a brush-like so-called "magnetic brush", which will exert a certain pressure on the surface of the workpiece. .
When the workpiece is placed in this magnetic field, the "magnetic brush" generates a magnetic force and acts on the surface of the workpiece in the form of pressure. When the workpiece performs the rotary motion and the axial motion, a relative motion occurs between the magnetic abrasive brush and the workpiece, thereby grinding the inner bore surface of the workpiece.
During the magnetic grinding process, the single abrasive particles, under the combined action of the magnetic field force, the magnetic field holding force and the tangential friction force, keep the abrasive particles stably in the polishing area, and achieve the grinding and polishing of the workpiece surface.
At the same time, due to the magnetic field force, the abrasive particles will automatically collect into the polishing area and collect on the inner surface of the workpiece to be polished to form a complete polishing cycle.
Figure 2 shows the surface morphology of the inner hole diamond coating before and after magnetic polishing. It is obvious that the polished sample becomes smooth and flat, and the grain removes the sharp corner of the outer end to achieve a desired effect.
The surface roughness of the diamond film decreased from Ra0.4543μm in Process A to Ra 0.1078 μm in Process B.
Figure 3 shows the surface morphology of the diamond film at different positions on the inner hole of the mold after polishing. It can be seen from the figure that the diamond film is smooth and flat, the particles are smooth and the finish is high. Especially the sizing belt and the working cone.
Figure 4 is a cross-sectional view of the inner diameter diamond film of the drawing die at different positions. It can be seen from the figure that the thickness of the diamond film at each position is uniform.
As can be seen from the figure, the diamond film on the surface of the inner hole has a distinct diamond characteristic peak.
The quality of the diamond film at the working cone is better than that of the diamond film at other locations. There is no obvious peak except for the diamond characteristic peak at 1332 cm-1.
There is also a certain graphite peak at the sizing belt and the outlet cone. It may be because the position of the hot wire is too close or too far, and the quality of the diamond is not very pure.
It can be seen from the Raman spectrum at different positions on the surface after polishing the inner hole that the diamond film deposited on the surface of the inner hole has good overall quality after polishing, and the diamond peak deviates from the standard peak of 1332 cm-1, indicating that The internal stress of the film is not large, and the adhesion of the diamond film can be better ensured.
in conclusion
Polishing the surface of the diamond coating with magnetic grinding can effectively remove the sharp corners of the outer end of the grain without causing damage to the coating, affecting the adhesion of the coating, and achieving a desired effect, thereby breaking the surface roughness of the conventional diamond film. The difficulty of polishing, the bottleneck of the coating drawing mold can not meet the needs of practical applications, and is of great significance for the industrialization of CVD diamond coating technology.
Honeycomb Cellular Blinds Shades
Motorized honeycomb cellular shades is in their specially honeycomb shape that air cell of a unique construction , Motoried Honeycomb Shades blocks harmful UV rays , provide perfect level of privacy and excellent insulation from outdoor to indoor room. Motorized cellular shades offers superior energy efficiency, keeping inside room temperature to achieve home warmer in the winter and cooler in the summer .
Honeycomb Cellular blinds has a wide range of uses and diversified operation, the two most popular modes are Electric Top Down & Bottom Up honeycomb blind and Automatic Day / Night cellular blinds, two of blockout shades and filtering light shade are in one, to the greatest extent possible to meet the requirement of consumer. Honeycomb Cellular blinds is perfect skylights window treatment , it provide one or more insulation layers that keeping heating and cooling air inside room .
Key Features
Operating System
It is easy to find out Operating system for Cellular shades. Top Down/ Bottom Up cellular blind, or Day / Night Cellular shades whateven you like. Motorized honeycomb cellular blinds would be a very worthwhile investment operation system , it is more convenient and easier .
Largest Selection
Explore the widest selection of cellular pleat sizes , semi opaque and opacities , colors , textures . Honeycomb shadings can also meet many specialty shaped windows .
Energy-Efficiency
Studies show that windows are responsible for up to 50% of your home`s energy losses . Honeycomb cellular shade trap air in distinct pockets , creating exceptional insulation . helping lower energy consumption and bills .
Room Darkening
Blockout Cellular blinds offer unparalleled darkness . The secret lies within exceptional insulation material , optimized to absorb or deflect nearly all incoming room light .
Sound Absorption
Improve your room`s acoustics while reducing the intensity of outside sound. Honeycomb Shade absorb up to 70% of sound energy , creating a more quiet .
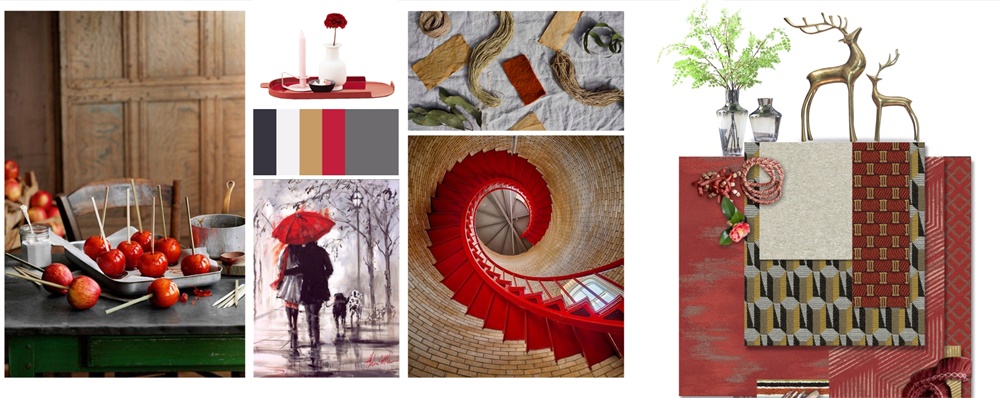
Cellular Honeycomb Shades Blinds
Motorized Window Cellular Shades,Insulated Layer Honeycomb Shades,Remote Control Cellular Blind,Automated Cellular Blinds
Shenzhen Yuaneng Industrial Co.,Ltd , https://www.bi-colour.com