The DMG MORI with the C and Y axes and the power knife NLX 2500 was selected by Buchholz Hydraulic as a turning solution.
Founded in 1884 in Buch, Germany, Buchholz originally manufactures handmade products. Since 1959, Buchholz Hydraulik has become a company specializing in solution development and production of mobile hydraulic system control valves. The medium-sized company has more than 300 employees on three continents serving a wide range of industry customers, including construction machinery and automotive manufacturing, as well as shipping companies. Buchholz Hydraulik's production equipment requires high-quality and high-performance CNC machines to meet the demands of high productivity. In October 2014, their lathe department installed a DMG MORI NLX 2500|700 with C-axis and Y-axis for complete machining of complex workpieces. In addition to the new DMG MORI design, the easy-to-use user interface CELOS ® enhances the operating comfort and ease of operation of the turning center.
Forklifts and excavators are just two examples of hydraulic solutions in many industrial applications. Buchholz Hydraulik's commitment to customer orientation has made them a competitive partner for development, offering projects from idea to trial and optimization of the entire process in the car. At the heart of the job is to meet every product solution that customers need, including functional and cost requirements.
Over the years, Buchholz Hydraulik has always adhered to the high quality of its products as well as customer-oriented order processing, including fast delivery services. This high standard is guaranteed by highly trained staff and innovative machine technology. Complete processing is the key, because this production method can meet the requirements of high productivity. In addition to a variety of automation systems, Buchholz Hydraulik has recently upgraded its lathe technology to replace the old 2-axis lathe with DMG MORI's NLX 2500|700 turning center.
CELOS ® and new style design optimize operating comfort
The NLX 2500|700 is produced by Gitemai Italy and is supplied to the European market. It is equipped with a wide range of expansion options and is therefore perfectly suited to the application requirements. Buchholz Hydraulik uses turning centers with countershafts, C and Y axes and power knives. "This way, we can turning and milling work, but also processing front and back," processing technical director Heiko Ne ß ler explains. Productivity has increased dramatically compared to previous solutions. “The reason is simple, we don’t need a second machine that performs milling.â€
Another attractive new feature for Buchholz Hydraulik is the user interface of the NLX 2500|700. Since last year, DMG MORI has been equipped with CELOS ® and 21.5" ERGOline touch screens for machine tools. The user interface simplifies operation and DMG MORI also enhances functionality with advanced software and hardware. Heiko Ne ß le at MAPPS V The system writes the task order directly in the underlying user interface - usually programmed at the same time. One of the main advantages of CELOS ® is its 3D simulation of the program: "The simulation reminds us of possible collisions and calculates the machining time of the workpiece. "This option can calculate and arrange other work plans .DMG MORI new style design also improves the NLX 2500 |. 700 operating convenience of" bigger machine door allows the operator to easily close processing zones ", Heiko Ne ß ler says .
Buchholz Hydraulik for NLX 2500 | spoke highly of CELOS ® 700 and a new user interface: the machine has become an indispensable part of daily production. The conclusion of this conclusion is that they will install two more NLX 2500|700 machines in the coming months.
Since 1959, Buchholz Hydraulik has focused on solution-oriented development and production of mobile hydraulic control valves.
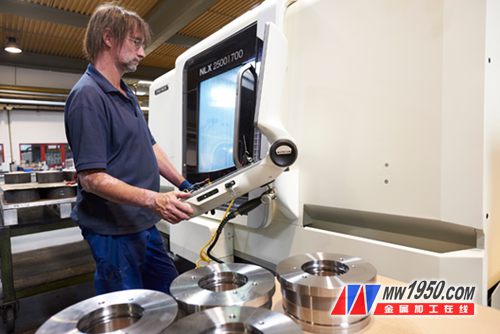
In October 2014, their lathe department installed a DMG MORI NLX 2500|700 with C-axis and Y-axis for complete machining of complex workpieces.
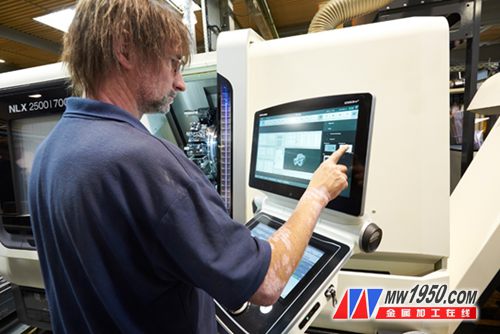
NLX2500 | 700 CELOS
® with a modern user interface and convenient operation of the 21.5 "ERGOline touch screen.
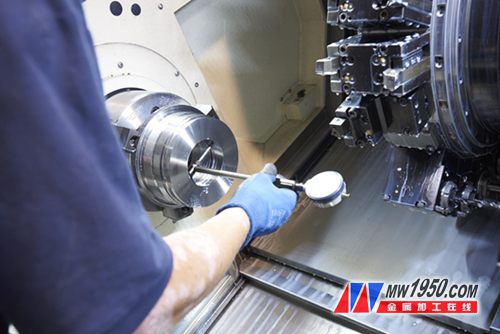
DMG Mori's new style design ensures the user's most convenient access to the processing area. 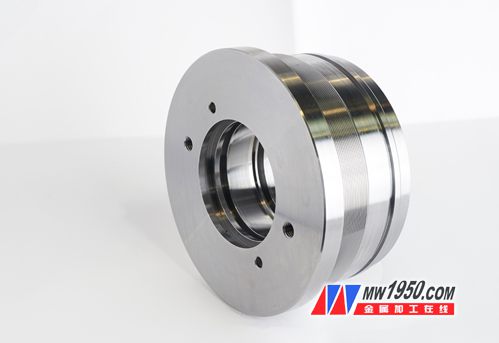
Buchholz Hydraulik also uses the NLX 2500|700 to produce complex turning/milling parts for hydraulic solutions. Diamond Wire For Silicon Cutting
The advantages of Diamond Wire cutting
technology are huge, and it can replace the traditional mortar wire. Diamond
wire is mainly used in the cutting of hard and brittle materials such as
crystalline silicon and sapphire. Compared with traditional mortar steel wire
cutting, it has high efficiency (4-5 times the cutting speed), less loss and
high chip yield (15-20% more silicon). The advantages of low environmental
pollution (no organic liquid) and high product quality. Among the diamond wire,
electroplated diamond wire is widely favored by the market for its outstanding
advantages of low wire consumption per piece, small wire diameter and high
cutting efficiency, and is superior to resin diamond wire.
Diamond Wire For Silicon Cutting,Silicon Cutting,Diamond Wire For Silicon,Diamond Wire Sawing For Silicon
Jiangyin Baoneng Precision New Material Co.,LTD , https://www.baonengwire.com