The general process of
PEEK injection molding is as follows:
1. Drying: The particulate polymer generally absorbs 0.5% w/w of atmospheric moisture. For best results, it should be dried until the moisture is less than 0.02% w/w. The material can be placed in an air circulating oven, dried at least at 150 ° C for 3 hours, or dried at 160 ° C for 2 hours. If it is dried in a dry box, the thickness of the raw material in the tray should not exceed 25 mm and prevent contamination.
2. Recycling: The remaining material can be recycled and injected into pure materials. It is recommended that the recycled material without filler should not exceed 30% of the total weight, and the recycled mixture containing the filling should not exceed 10% of the total weight.
3. Thermal stability: If the equipment is shut down during the melting process and the polymer residence time does not exceed 1 hour, there is no significant degradation of the material at a temperature of 360 °C. However, if the downtime exceeds 1 hour, the temperature of the cylinder should be reduced to 340 °C. At this temperature, the material can be kept stable for several hours. When the processing is continued, the temperature of the cylinder must be increased. If the downtime is more than 3 hours, The cartridge should be cleaned. Materials which are stable at 380 ° C, such as polyether sulfone or polyetherimide, can also be cleaned with low MFI polyethylene.
4. Injection machine: The melting point of the polymer is 343 ° C, which can be applied to traditional machines that can keep the melt temperature at 360-400 ° C.
5. Cartridge capacity: Due to the high processing temperature of the PEEK polymer, the residence time of the material must be as short as possible. The ideal barrel capacity is 2-5 times the total shot weight.
6. Nozzle and latching system: The melting point of the polymer is very high. If the temperature drops below 343 °C, the melt will solidify very quickly. Therefore, it is necessary to install a heater large enough at the nozzle to prevent the "cooling of the injection molding" from being caused by the cooling.
7. Screw: It is recommended that the minimum length-to-diameter ratio L/D of the screw is 16:1, but the L/D ratio between 18:1 and 24:1 should be preferred.
8. Barrel temperature: The unreinforced level is 360-380 ° C, and the enhanced level is 380-400 ° C.
9. Mold temperature: The surface temperature of the mold is 175-205 °C.
10. Injection pressure: The general injection pressure is 70-140 MPa.
11. Injection speed: medium to high speed.
12. Back pressure: It is recommended that the back pressure be set to 0-1.0 MPa (0-10 kgf/cm2).
13. Screw speed: The general screw speed is 50-100 rpm. For the reinforcement level, it is recommended to use a lower screw speed.
14. Mold shrinkage: Different grades of polymer have different shrinkage rates, the unfilled grade is about 1.2-2.4%, and the fill grade is: 0.1-1.1%.
15. Secondary processing: secondary processing such as bonding, tapping, press-in, metal inserts, cutting and surface metallization.
Twist Drill Bit
The twist drill is a Tool used to drill round holes in the workpiece by rotating cutting with a relatively fixed axis. Because of its chip slot into a spiral shape and the shape of the twist named. Spiral grooves have 2, 3, or more grooves, but 2 grooves are the most common. The twist drill can be clamped on manual or electric hand-held drilling tools or on drilling machines, milling machines, lathes or even machining centers. The bit material is usually high speed tool steel or hard alloy. Standard twist drill: The twist drill consists of the shank, neck and working part
We have five different materials,HSS-CO8%,HSS-CO5%,HSS-M2,HSS-4341,HSS-4241.From left to right there are from high quality to low quality.
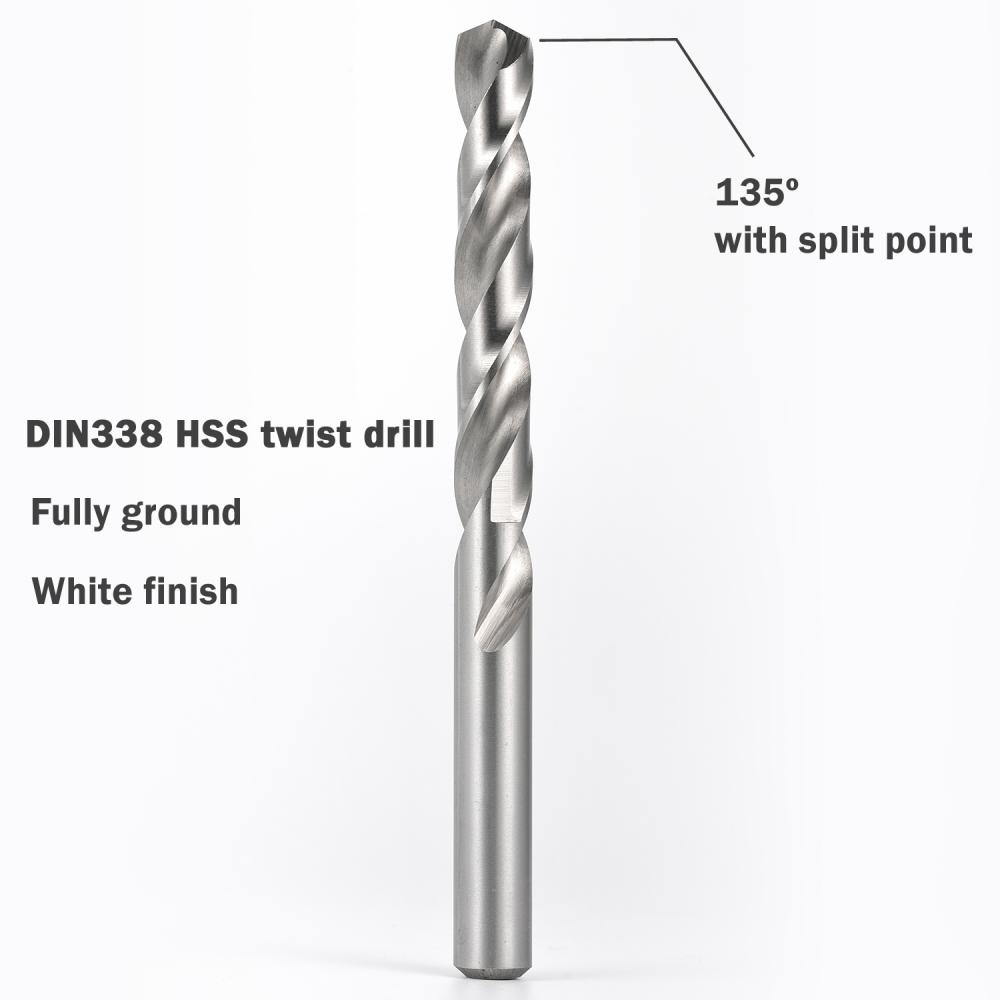
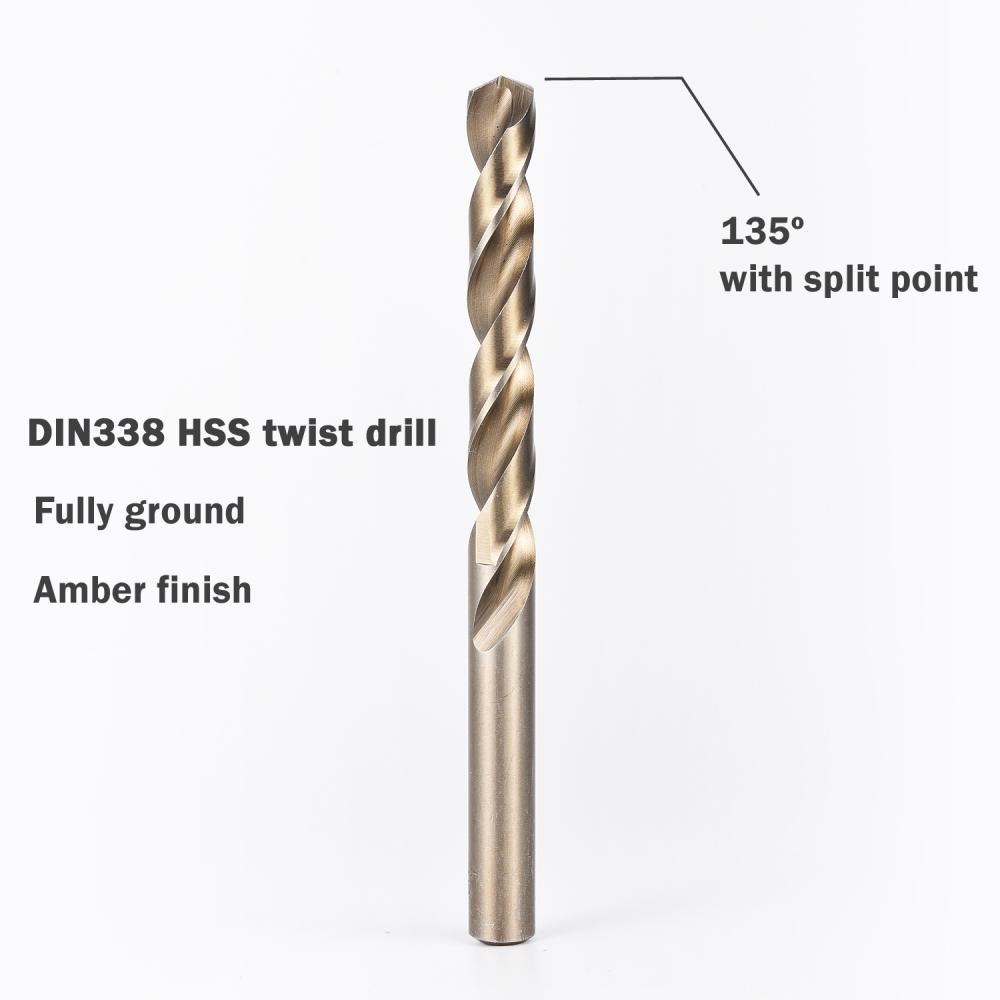
Twist Drill Bit,Glass Cutting Drill Bit,Long Metal Drill Bits,Electric Drill And Bits
Behappy Crafts (suzhou)Co.,Ltd , https://www.jshaoyue.com