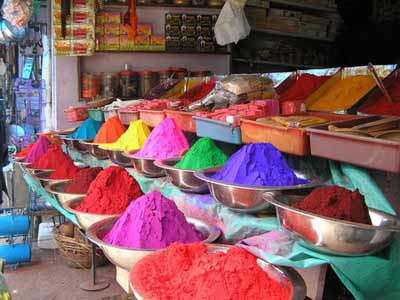
The situation facing the dye industry in China is still grim, and the internal and external environment is also very complicated. On the one hand, there is no fundamental change in the international market environment, and the global structural adjustment needs to continue for a long period of time, especially in the case of a global profit reduction phenomenon in the dye industry, due to the lower purchasing power of foreign demand customers, China’s large Some dye companies have encountered difficulties in exporting their products and achieving the expected growth targets.
The green transformation of the dye industry essentially reduces the energy and resource consumption in its production process and reduces pollutants and greenhouse gas emissions. At present, in the dye production process, there are many raw materials consumed, and the material consumption per ton can reach several tons to several tens of tons. At the same time, in the production process, one or more water washings are often required, and the amount of water required is particularly large, resulting in a large number of By-products or wastes, especially effluents, are produced in large amounts. For example, reactive dyes are the most popular dyes for cellulosic fibers. The world's annual output has accounted for about 20% of the total amount of dyes. It ranks first in the dyes for cellulose fibers, but the utilization of reactive dyes is currently high. It is not high, generally 60~65%, and the widely used gap type inhalation dyeing process has a longer processing time after dyeing, including time for washing, neutralizing, soaping, and fixing, etc. The 1/3, not only takes a long time, consumes high energy, consumes much water, but also produces a large amount of intractable colored salty sewage. In addition, dyes and dye intermediates waste water refers to the process wastewater discharged during the production of dyes or dye intermediates, with high cod concentration. The basic raw materials for dye production are benzene, naphthalene, and guanidine, as well as aniline, nitrobenzene, and phenols. The loss of dyes results in high COD concentrations in water. For example, the wastewater cod discharged from a workshop of a dye factory in Inner Mongolia was as high as 170,000 mg/l.
As far as dyes and dye intermediates chemicals are concerned, their water consumption and sewage discharge volume are the most important constraints for their development. Therefore, dye enterprises not only wear hats with high energy consumption and high pollution for a long period of time, but also are the focus of local governments on energy conservation and emission reduction. In this respect, the pressure on dye enterprises has been relatively large. If this is not done well, it may be Eliminating the outflow will directly affect the survival and development of the company. In particular, the dye industry is currently facing tremendous pressure.
Therefore, green transformation has become a prerequisite for the development of the dye industry. Only a green transformation can achieve sustainable development. Of course, the key to green transformation is how to make energy-saving emission reductions and cross the threshold of energy conservation and environmental protection.
As the industry enters a transitional period, it requires an objective transformation of the enterprise and a transition to clean green. The companies that can survive in the market in the future must all be companies with good clean production and good energy-saving and emission-reduction technologies. This requires good articles on clean production. Cleaner production means the use of environmentally friendly production processes in the dye production process. Not only does the energy consumption in the production process decrease, but also the “three wastes†emissions decrease. The benefits of industrial green transformation are enormous. On the one hand, it is direct income. Direct benefits refer to energy costs that are reduced due to energy conservation. Indirect benefits include avoiding technological lock-in, improving the trading environment and trade conditions, promoting the development of energy-saving and environmental-friendly industries, and generating health benefits.
In the long run, what direct economic benefits will the industrial transition achieve? Overall, whether it is more cost-effective or more effective? CEO of a dye company in Shandong said that in the past two years, the company has been implementing production according to the requirements of cleaner production processes. management. “In the past, the production of 1 ton of dyes would result in the discharge of 30 tons of wastewater. Now that we have implemented cleaner production and technological innovations, we have been able to compress wastewater to within 10 tons. In the past, large amounts of waste alkali were generated during the production process, and clean production technology was applied. On the one hand, the waste acid and alkali produced in the production process itself will be reduced, and on the other hand, the waste acid and alkali produced will also be recovered and reused. By improving the process to implement clean production, the production efficiency will be increased, the cost will be reduced accordingly, and the pollution The emission of pollutants has been significantly reduced, which has reduced the pressure for energy conservation and emission reduction.†Practice has proved that cleaner production has reduced our costs and increased the gross margins to a certain extent. Not only has the utilization of resources been improved, but also production efficiency has increased. Economic benefits, but also significantly reduce emissions of waste, thereby greatly reducing the environmental pollution and impact. These advantages are enough to allow us to have the right to speak in the market competition." The boss said. Therefore, the transition to a green economy is the basis for the sustainable development of the dye industry.
Lunch Bags,Insulated Lunch Tote Bags,Reusable Portable Lunch Bag,Neoprene Lunch Bags
Dongguan C.Y. RedApple Industrial Limited , https://www.hpgbags.com