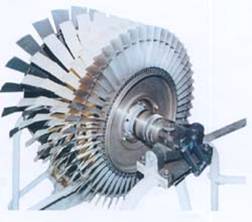
At this stage, most aero-engine parts are made of titanium alloy materials. According to the assembly requirements, precision machining of surface finish and surface roughness all require grinding to ensure the surface quality of the parts. Due to the physical and mechanical properties of titanium alloy materials, surface burns and surface integrity are reduced during the grinding process. At present, it is urgent to solve the problem of grinding titanium alloy materials. Therefore, it is necessary to select the appropriate grinding wheel.
The types of titanium alloys are broadly classified into three types, α titanium alloys, β titanium alloys, and α+β titanium alloys. It has a small specific gravity, high specific strength, high temperature resistance, corrosion resistance, super memory, no magnetic properties, low elastic modulus, and biocompatibility number. This series of excellent materials enables its application in a wide range of fields. Titanium has a melting point of 1668°C and a boiling point of 3400°C, which is higher than that of ferronickel. Therefore, light heat resistance has become an excellent basis for long-term work at 500°C. The long-term working temperature of the new titanium alloy is even higher. Its strength is 10 times higher than that of aluminum alloy at 300-350°C. The strength of commonly used α+β titanium alloys reaches 1.2 GPa, the specific gravity is 0.44 MPa, and the specific strength is 23-27, which is higher than that of alloy steels. The tensile strength of titanium alloys can exceed 1.5 GPa and must be applied with a great deal of force. It is a typical hard-to-machine material. The thermal conductivity coefficient of titanium is 0.036cal, and the thermal conductivity of TC11 titanium alloy is even worse. The modulus of elasticity of titanium is about 1/2 of that of steel, and its elasticity during processing is large and it is easy to vibrate.
Titanium alloys contain oxygen, hydrogen, nitrogen, carbon, and sometimes include impurities such as silicon and iron. These elements undergo a strong reaction and are present in the lattice in interstitial form, which can increase the strength of the titanium alloy and reduce the plasticity, even Fracture toughness, low temperature toughness, fatigue strength, corrosion resistance, cold forming and weldability deteriorate. Titanium alloys are highly chemical at high temperatures. At a certain grinding temperature, titanium forms an oxidized, nitrided protective film, which makes the surface layer hardened and brittle, reduces the elasticity, increases the degree of work hardening, and is easy to attach when grinding. , Clogging of the grinding wheel causes the grinding to overheat and the surface integrity to decrease.
Titanium alloy grinding requires that the grinding wheel has small adhesion, small wear, hard to plug, and low grinding temperature. This mainly includes the size and shape of the abrasive grain binding agent. Ordinary Grinding Wheels consist of abrasive binders and pores. The abrasive action is to grind the processed material to form the desired surface. The effect of the bonding agent is to bond the abrasive together to form a certain shape and hardness, so that the abrasive particles can maintain a stable movement trajectory during the grinding process and can be self-releasing. The pores are evacuated during the grinding process, and the cooling has both lubrication effects. Common abrasives include corundum series (aluminum oxide), and silicon carbide series. Grinding titanium alloy should be chosen silicon carbide grinding wheel.
The binder is divided into two kinds: resin and ceramic: 1) The ceramic binder has strong particle, good thermal stability and chemical stability, waterproof, heat resistance, corrosion resistance, small wear, long-term grinding performance, porosity, not easy Blockage, high productivity. Brittle, can not withstand a large impact load. 2) The resin bond abrasive wheel has high strength, elasticity, good impact resistance, poor thermal stability, poor corrosion resistance, and will lose its strength due to high temperatures.
When grinding titanium alloys with silicon carbide and alumina grinding wheels, the grinding debris is easily attached to the surface of the grinding wheel, grinding force is large, and the grinding wheel wears badly, resulting in a decrease in the surface quality of the workpiece.
1) The relationship between grinding force and grinding parameters. Choosing reasonable grinding parameters to control the grinding force and then improving the grinding quality is the key to the grinding of titanium alloys. The grinding force in the grinding process of titanium alloys consists of cutting and friction. The proportion of possession varies. The chip deformation force in the grinding of titanium alloys is the main one, accounting for about three times as much friction as the grinding force. However, compared with the general metal materials, the proportion of friction is much greater. This has a great relationship with the properties of titanium alloy materials. Titanium alloy has a small elastic modulus, low thermal conductivity, high chemical activity, and stickiness and toughness. The grindstone adheres severely during grinding, resulting in increased friction. The friction force is affected by the linear speed of the grinding wheel and is greatly affected by the grinding depth. Therefore, it is necessary to control the grinding force by adopting proper grinding depth and grinding line speed. The friction coefficient of titanium alloy increases with the increase of the linear velocity. In tribology, the relationship between friction coefficient and relative slip. Only when the load increases, does the friction coefficient increase with the increase of the sliding speed. In grinding, each abrasive grain receives considerable stress. All friction coefficients are greatly affected by changes in grinding parameters.
2) Linear relationship between chip deformation force and grinding depth Due to the size effect, starting from the basic principle of fracture mechanics, the grinding process is actually a crack expansion process. The size effect is mainly caused by the chip deformation force in the grinding force. The relationship between the metal removal rate and the normal grinding force actually depends not only on the dressing of the workpiece material and the grinding wheel, but also because of the size effect.
3) The grinding depth has a great influence on the metal removal ratio, which is due to the size effect. The influence of the workpiece speed is much smaller, so that the normal force and the metal removal ratio are nonlinear.
To sum up the above: Grinding titanium alloy material should choose grinding parameters: speed 45M/S, cutting depth 0.01-0.02mm.
Titanium alloy grinding process has a more serious grinding wheel adhesion, grinding force and grinding temperature are high, it is easy to produce grinding burns and cracks. When grinding titanium alloys with ordinary abrasives, even if the grinding depth is small, grinding burns and cracks may occur on the grinding surface. Appearance is yellow-brown spots, hairline cracks, and its direction is perpendicular to the grinding direction. If the amount of grinding is large, there will be scaly folds and plastic deformation of metal deposits on the surface. What are these substances? Let's take a look at the silicon carbide abrasive grain grinding titanium alloy so that the chemical reaction formula: SiC + Ti → TiC + Si. Let us take a look at the oxidation reaction of silicon carbide abrasive particles at a certain atmospheric temperature: SiC+2O2→SiO2+CO2.
Some of the carbon atoms will diffuse toward the surface of the workpiece being ground. Under the effect of sliding shear force, the SiO2 oxide film will peel off, causing oxidative wear of the SiC abrasive particles, leaving a diffusion layer of oxygen and carbon on the surface of the workpiece. The surface of the abrasive grain loses its carbon-weakening layer, the hardness of the SiC grain decreases, the grinding force increases, the wear of the grinding wheel increases, and the grinding temperature rises. From the microscopic point of view, the process of formation of abrasive particles and adhesion is that the cutting edge first appears a small area of ​​adhesion and a large area of ​​adhesion, and the abrasive particles are finely broken, and then the abrasive particles break and fall off, and the titanium alloy grinding zone undergoes plastic deformation. The abrasive particles and the workpiece are bonded to each other. This has both physical adsorption and chemical adsorption. With the relative shearing shear force, the processed material is transferred to the abrasive particles. This is the entire process of the wheel adhesion.
This article through the above analysis of titanium alloy material properties, grinding force, grinding parameters and how to choose a new type of abrasive wheel, and finally through the actual part of the repeated processing, from the actual out of the actual processing of titanium alloy grinding wheel, after processing To ensure the surface integrity of the parts, to solve the titanium alloy grinding problem and improve the production efficiency. This is only a preliminary summary and discussion of the titanium alloy material (TC11), and it is hoped that the titanium alloy material will be helpful in grinding aviation products.
Glass bits have a spade-shaped carbide point, used to drill holes in materials of glass, ceramics,etc. They generate high temperatures and have a very short life. Holes are generally drilled at low speed with a succession of increasing bit sizes. Diamond drill bits can also be used to cut holes in glass, and last much longer.
It is an alloy triangular bit mounted on the ordinary Electric Hand Drill, which has high hardness, sharp blade and good precision, and is specially used for opening holes in ceramic tiles. But the drill wears too much into concrete to be used on concrete.
Ceramic Tile Bit,Ceramic Drill Bit,Drilling Through Tile,Ceramic Tile Drill Bit
Behappy Crafts (suzhou)Co.,Ltd , https://www.jshaoyue.com