Large blast furnace gas full dry bag dust removal technology
The blast furnace gas dry bag dust removal technology is an important technological innovation for energy saving, emission reduction and clean production in the 21st century blast furnace. It can significantly reduce the new water consumption and reduce environmental pollution in the ironmaking production process, and has become the development direction of modern blast furnace ironmaking technology. The blast furnace gas dry bag dust removal technology has been developed for more than 30 years. In January 2007, China's self-developed blast furnace gas full dry low pressure pulse bag dust removal technology was successfully completed in Qiangang No. 2 blast furnace (2650m3), completely eliminating the standby gas wet dust removal system. Research and development of gas temperature control, dust-removing ash dense phase pneumatic conveying, pipeline system anti-corrosion and other core technologies, so that China's large-scale blast furnace gas dry bag dust removal technology has reached the international advanced level.
Optimize integrated process and system configuration
Through research and analysis of domestic and international blast furnace gas dry bag dust removal technology application practice, the pressurized gas back-blowing dust removal technology and low-pressure pulse dust removal technology were systematically compared and researched, and the blast furnace gas full dry low-pressure pulse bag dust removal process was designed and developed. Qiangang No. 2 blast furnace adopts 14 dust-removing tanks with a diameter of 4600mm. The tanks are arranged in a double-row arrangement. The two columns of tanks are equipped with waste gas and net gas pipelines. The gas pipelines are designed according to the principle of equal flow velocity, so that they can enter each tank. The gas quantity is evenly distributed, the whole system is compact in process, the process is short and smooth, and the equipment is easy to maintain and maintain. The low filtration rate design concept ensures safe and reliable system operation. Each box is provided with 250 filter bags, the filter bag size is <160mm×7000mm, the single box filter area is 880m2, and the total filter area is 12320m2. In the design, the diameter and length of the filter bag are increased, the height-to-diameter ratio is reduced, and the structure of the filter bag is more reasonable. The diameter of the box is enlarged, the treatment capacity of the dust removal unit is improved, the number of cabinets, construction investment and floor space are reduced. . Table 2 is the technical parameters of the whole dry bag dust removal process of No. 2 blast furnace gas of Qiangang.
Gas temperature control technology
Gas temperature control is a key element of bag dust removal technology. Under normal conditions, the gas temperature should be controlled at 100-220 °C. The gas temperature is too high or too low, which will affect the normal operation of the system. The gas dry bag dust removal technology is adopted, and the blast furnace operation should pay more attention to the adjustment control of the furnace top temperature. When the temperature of the furnace top rises, the furnace top atomization water spray cooling measures are taken. At the same time, a heat pipe heat exchanger is arranged on the blast furnace waste gas pipeline, water is used as a cooling medium, and the heat of the high temperature gas is transmitted through the heat pipe, so that the water vaporizes and absorbs the gas heat. It can effectively solve the technical problem of high temperature control of gas. The low-temperature control of the gas should adopt technical measures such as improving the quality of the raw fuel in the furnace, strengthening the monitoring of the cooling equipment of the furnace, reasonably controlling the temperature at the top of the furnace, and maintaining the insulation of the waste gas pipeline. In the blast furnace, the effective measures should be taken to reduce the gas. The water content controls the gas temperature above the dew point. At present, it is researching and developing high-efficiency and rapid heat transfer technology for low-temperature gas, so that high-temperature and low-temperature gases can be effectively controlled.
On-line monitoring technology for gas dust content
The online monitoring device for dust content of gas is an important testing device for monitoring the operation of the blast furnace gas bag dust removal system. The on-line monitoring system for dust content of blast furnace gas research and development adopts the principle of charge induction. In the flowing powder, the particles and the particles, the particles and the wall of the tube, and the particles and the bag are electrostatically charged due to friction and collision, forming an electrostatic field, and the change of the electrostatic field can reflect the change of the dust content. The online monitoring system of gas dust content determines whether the bag dust removal system is operating normally by measuring the change of static charge. When the bag is damaged, the gas and solid two-phase flow dust content in the pipeline increases, and the static charge intensity increases. The sensor inserted into the output pipe of the tank can detect the charge amount in time and output it to the transmitter to realize the gas content. Automatic monitoring of dust volume [2]. The sensor surface of the online monitoring device for the dust content of No. 2 blast furnace gas of Qiangang is made of special coating material, which avoids the adhesion of dust on the sensor surface due to water content in the blast furnace gas, thereby improving the detection accuracy and stability of the device and solving the large blast furnace. The technical problem of online monitoring of dust content in gas dry dedusting system.
Gas pipeline system anti-corrosion technology
Production practice found that the use of blast furnace gas dry bag dust removal technology, the chloride ion content in the net gas increased significantly. This is mainly due to the formation of gaseous HCl in the blast furnace smelting process due to the halide in the blast furnace raw fuel. When the gas temperature reaches the dew point, the gaseous HCl combines with the condensed water to form hydrochloric acid. Through the analysis and analysis of the gas condensate, the pH value is lower than 7, sometimes even 2 to 3, which is strongly acidic, and is highly corrosive to the gas pipeline and the corrugated compensator, causing abnormal corrosion of the gas pipeline system. In order to prevent the abnormal corrosion of the gas pipeline system, the material and structure of the gas pipeline corrugated compensator were technically improved. The material was improved from 316L to 800 series, which improved the anti-corrosion performance; the inner wall of the gas pipeline was treated with anti-corrosion coating; on the net gas pipeline Technical measures such as spraying lye or water spray system were set up, and after one year of production practice, remarkable results were obtained.
Dust ash dense phase pneumatic conveying technology
Independent research and development of dedusting ash dense phase conveying technology, using nitrogen or purified gas as carrier gas to transport dust removal ash, solving a series of technical defects of traditional mechanical ash conveying process, optimizing the process flow, reducing energy consumption, reducing two Secondary pollution has overcome technical problems such as wear of ash pipelines.
Http://shbuxiugang.5jw.cn/index.aspx
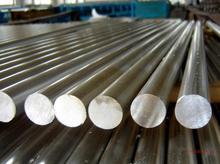
Smart Faucet,Smart Faucet Price,Smart Faucet Product
Yuyao Zelin Sanitary Ware Co., Ltd , https://www.kitchen-sinkfaucet.com