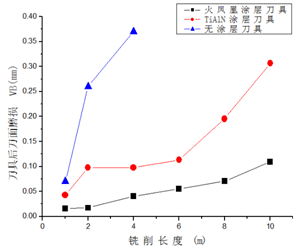
Coating method
There are currently two coating methods commonly used in production: physical vapor deposition (PVD) and chemical vapor deposition (CVD). The former has a deposition temperature of 500 ° C and a coating thickness of 2 to 5 μm; the latter has a deposition temperature of 900 ° C to 1100 ° C, a coating thickness of 5 to 10 μm, and a simple device and a uniform coating. Since the PVD method does not exceed the tempering temperature of the high-speed steel itself, the high-speed steel tool generally adopts the PVD method, and the hard alloy is mostly the CVD method. When the cemented carbide is coated by CVD, due to its high deposition temperature, a brittle decarburization layer (η phase) is easily formed between the coating and the substrate, resulting in brittle fracture of the blade. In the past decade or so, with the advancement of coating technology, the cemented carbide can also adopt the PVD method. In foreign countries, a composite coating process, called PACVD (plasma chemical vapor deposition), has been developed using a combination of PVD/CVD techniques. That is, using plasma to promote chemical reaction, the coating temperature can be lowered to below 400 ° C (the current coating temperature can be reduced to 180 ° C ~ 200 ° C), so that there is no diffusion between the cemented carbide substrate and the coating material. , phase change or exchange reaction, can maintain the original toughness of the blade. This method is reported to be particularly effective for coating diamond and cubic boron nitride (CBN) superhard coatings.
When coating by CVD method, the cutting edge needs to be passivated in advance (the blunt radius is generally 0.02~0.08mm, and the cutting edge strength increases with the radius of the blunt circle), so the blade has no sharp edges. Therefore, the PVD method should be used for tools that produce thin chips for finishing and require sharp cutting edges. In addition to being applied to conventional cutting inserts, the coating can be applied to integral tools and has been developed to be applied to welded carbide tools. According to reports, a foreign company used the PCVD method on the welded cemented carbide drill bit. As a result, the drill life of the steel material was 10 times longer than that of the high-speed steel drill bit, and the efficiency was increased by 5 times.
Various new coatings introduced by King Kong
Coating color hardness HV thickness μm friction coefficient maximum use temperature °C Description
ZrCN composite blue ash 25001-40.3550 is highly versatile
TiN single layer golden 23001-40.4500 cost-effective coating
TiAlN composite purple 32001-40.5800 is highly versatile
AlTiN composite black 34001-40.5900 high speed, high hardness processing
TiAlCrN sub-black 35001-40.61000 special processing field
TiCN gradient gray black 30001-40.4400 high toughness universal coating
CrN gradient silver bright 20003-150.5700 for processing copper, titanium, mold
DLC black color 1000~40000.5-20.05400 is suitable for non-ferrous metals, graphite, plastic
Coating material
The coating material must have high hardness, good wear resistance, stable chemical properties, no chemical reaction with the workpiece material, heat and oxidation resistance, low friction factor, and strong adhesion to the substrate. Obviously, a single coating material is difficult to meet the above requirements. Therefore, the hard coating material has been initially coated with only a single TiC, TiN, Al2O3, into the new stage of developing thick film, composite and multi-component coatings. Newly developed TiCN, TiAlN, TiAlN multi-component, ultra-thin, ultra-multi-layer coatings combined with TiC, TiN, Al2O3 coatings, and a new plastic deformation resistant matrix to improve coating toughness, coating and matrix Significant progress has been made in the bonding strength and the improvement of the wear resistance of the coating. At present, it has broken through the technology of coating diamond film on the cemented carbide substrate, which has improved the performance of the tool.
The most mature and widely used hard coating material is TiN, but the bonding strength of TiN to the substrate is inferior to that of TiC coating. The coating is easy to peel off and the hardness is not as high as TiC. When the cutting temperature is high, the film is easy to oxidize. Ablated. TiC coatings have high hardness and wear resistance, and good oxidation resistance, but they are brittle and not resistant to impact. TiCN combines the advantages of both TiC and TiN materials. It can control the TiCN properties by continuously changing the composition of C and N during the coating process, and form a multi-layer structure with different compositions, which can reduce the internal stress of the coating and improve the toughness. Increase the thickness of the coating, prevent crack propagation and reduce chipping. Therefore, some of the blades currently produced, such as the GC4000 series blades recommended by Sweden Sandvik for processing steel, the CN series blades produced by Zhuzhou Cemented Carbide Factory of China, and the T715X and T725X coated blades of Toshiba of Japan have TiCN coating. Layer composition. TiCN-based coatings are suitable for processing ordinary steel, alloy steel, stainless steel and wear-resistant cast iron. The material removal rate can be increased by 2 to 3 times when machining workpieces.
TiAlN, CrN, and TiAlCrN are new hard coating materials developed in recent years. TiAlN coated blades are commercially available. It has good chemical stability and oxidation and wear resistance. Its tool life can be 3-4 times higher than that of TiN coating when it is used to process high alloy steel, stainless steel, titanium alloy and nickel alloy. In addition, if there is a suitable aluminum concentration in the TiAlN coating, a hard inert protective film will be formed on the interface between the rake face and the chip during cutting. The film has better heat insulation and can be more effective. Ground for high speed cutting. For example, the H7 blade from Kennametal, USA, is a TiAlN coating designed for high-speed milling of high-performance materials such as alloy steel, high alloy steel and stainless steel. CrN is a titanium-free coating suitable for cutting titanium and titanium alloys, copper, aluminum and other soft materials with good chemical stability and no sticking. TiAlCrN is a gradient structure coating, which not only has high toughness and hardness, but also has a small friction factor. It is suitable for milling cutters, hobs, taps and other tools, and its cutting performance is obviously better than TiN.
A German company has developed the Supernitride coating series, in which the super titanium nitride coating has a high aluminum content and can form a stable oxide layer (oxidation temperature up to 1000 ° C), which is harder and more dense than the general TiAlN coating. Dense, more high temperature resistant, suitable for high speed cutting, dry cutting and hard cutting tools, can process hardened steel with hardness up to 58HRC.
In addition, the nano-ultra-film coating process has become increasingly mature. According to reports, a Japanese company has introduced a high-speed and powerful drill bit, which is coated with 1,000 layers of TiN and AlN ultra-thin film coatings on a tough K-type (WC+Co) cemented carbide substrate. About 2.5 μm. The use shows that the bending strength and fracture toughness of the drill can be greatly improved, the hardness is equivalent to CBN, and the tool life can be increased by about 2 times. The company has also developed ZX coated end mills with 2,000 layers of ultra-thin coatings, each with a thickness of about 1 nm. The 60HRC high-hardness material is machined with the end mill, and the tool life is much higher than that of TiCN and TiAlN coated tools. At the 8th China International Machine Tool Show (CIMT2003), a Swiss company introduced a nanostructured coating (AITiN/SiN) end mill with a coating hardness of 45GPa and an oxidation temperature of 1100°C. The cutting comparison test shows its life. It is 3 times higher than TiN coated end mills and 2 times higher than TiAlCN coated end mills. In addition to the above new coatings of AITIN/SiN and TiAlCN, there are also special coatings, such as MoS2 and DLC lubricated coatings, which have a small friction factor (0.05). They are suitable for coating tools such as taps and drills to improve chip removal. Performance, or as a surface coating for composite coatings, reduces chip adhesion.
We diviided the led light according to the using eviiroment. Most of our product is the commercial LED Lighting
Commercial lighting is a term used to describe lighting that is used in commercial spaces, including auto dealerships, distribution centers, churches, factories, offices, and warehouses. Unlike residential lighting, commercial lighting is made to withstand more abuse and has a longer lifespan.
While the focus of residential lighting is often on aesthetics, commercial lighting is task orientated. Commercial lighting systems are designed based on what the application is. For example, in an office-type setting, you may see task lighting, which illuminates specific areas where employees need concentrated light to be able to perform their jobs.
Suspend Linear Light,Linear Wall Sconce Lighting,Linear Wall Mounted Light Fixture,Linear Lights For Kitchen
Jiangmen Dilin Lighting High-Tech Co., Ltd. , https://www.dilinlight.com